Rapid Prototyping
Rapid Prototyping (RP) allows the manufacture of physical objects directly from 3-D computer models. It is an additive method, unlike CNC milling, with applications such as concept evaluation, architectural ornament, and light functional testing. RP is integral to many design processes. This report briefly investigates current Stereolithography, Fused Deposition Modeling, and 3D Printing technologies.
CONTENTS
1 Stereolithography (SLA)
Patented in 1986, Stereolithography is the oldest RP technique to generate objects from volumetric data. SLA is a highly accurate process
based on UV lasers and photo-curable liquid polymer that enables reproduction of detailed digital features. It is widely used for making
concept models, presentation designs, and patterns for investment casting. Raw SLA output usually comes with a smooth surface and can be
painted or electroplated.
All CAD models must be converted into STL format and 'sliced' into very thin layers. The pre-processing software also generates
auxillary support structures to ensure the successful manufacture of delicate design features. A basic stereolithography apparatus
consists of:
- An ultra-violet Laser and Scanner system;
- A Vat [filled with photopolymer];
- A movable Platform, or elevator.
During a build-operation, the photosensitive liquid inside the vat will harden on the surface where the laser has traced out a
cross-section of the digital design, thus forming a single layer of the future model. The platform supporting this model is
subsequently lowered by the thickness of one layer and recoated for the following pass. When construction is complete the object
is raised and allowed to drain. Post-processing includes removal of supports and curing inside an ultra-violet oven.
Stereolithography equipment has been sold by 3D Systems since 1988. The current Viper imaging system offers
dual-resolution part-building within a build-envelope of 250mm XYZ.
2 Fused Deposition Modeling (FDM)
Fused Deposition Modeling is an office-friendly prototyping technique for extruding physical objects from 3-D data. FDM applications include concept models and production parts for ergonomic testing. ABS plastic builds are uv-resistant, unlike stereolithography resins, more durable, come in several colours, and can be machined, sanded, and electroplated. Shape Deposition Manufacturing (SDM) combines layered manufacturing processes with welding and CNC-machining. FDM equipment consists of:
- A Plastic Filament supply coil and the Nozzle;
- A movable Platform [for the object];
- The enclosing machine chamber [to maintain operating temperature].
Fused Deposition Modeling uses the STL file format to convert CAD data into layers. The pre-processing software also generates a
temporary mount for the object, as well as support structures for delicate design features.
The exact toolpath of the extrusion nozzle is determined by each XY cross-section of the design, resulting in the successive layers of
heated thermo-plastic that will constitute the final object. Stratasys is a major manufacturer of FDM machines.
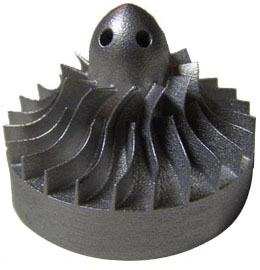
Photo: Bcn0209. GNU Free Documentation License.
3D-Printing (3DP)
3D-Printing is based on conventional ink-jet technology, powdered materials and liquid binders. 3DPTM has been used to generate shells,
metal tools, pharmaceuticals, and prototypes directly from 3-D data. High-load components are often sintered and infiltrated with
low-melting point alloys since 3DP enables local control over the structure and composition of the physical model.
A generic 3D-Printing device consists of:
- Ink-Jet heads and a Liquid Adhesive supply;
- the Build-Cylinder with a movable platform;
- the Powder Delivery System.
The path of the Ink-Jet head is determined by the current XY cross-section of the digital design being traced. Binder fluid is thus
combined with an amount of powder to form each layer, while the platform supporting the object inside the cylinder is lowered for
another pass.
3D Systems provide office-friendly printers with Multi-Jet-Modeling, replacement cartridges, and Ethernet access.
ZCorp 3-D Printers permit layer thickness adjustments and handle RGB colour management. ZCorp technology employs
plaster-based powders capable of resin infiltration. The versatility of 3DP is also exploited by ProMetal, a division of ExtrudeHone. Rapid metal prototyping involves
multiple print heads, metallic powders and a polymer binder, low-temperature curing, high-temperature sintering, and alloy infiltration
for increased durability.
4 Rapid Prototyping Technologies*
RP Technology | Sterolithography | Fused Deposition Modeling | 3D-Printing |
---|---|---|---|
Acronym | SLA | FDM (SDM) | 3DP, 3DPTM |
Manufacturer | 3D Systems | Stratasys | ZCorp |
Device name | Viper si2 | FDM Maxum | Z810 System |
Methodology | UV Laser | Extrusion Nozzle | Ink-Jet |
Materials | liquid polymer | thermoplastics, eg. ABS | plaster-based, starch-based |
Colours | material standard | 8 + 3 translucent | Grayscale and RGB |
Layer thickness | ~0.01mm - 0.7mm | ~0.18mm - 0.25mm | ~0.076mm - 0.254mm |
Support structures | Breakaway | Breakaway, watersoluble | not required |
Build-envelope | 250 X 250 X 250mm | 600 X 500 X 600mm | 500 X 600 X 400mm |
Equipment weight | 463kg | n.a. | 565kg |
* August, 2004
5 Conclusion
Rapid prototyping technologies like Stereolithography, Fused Deposition Modeling, and 3D-Printing support numerous industries -
automotive, electronics, medical - with patterns for investment casting, concept models, metal tools, and end-use parts.
Rapid Prototyping (also called Solid Freeform Fabrication) has diverse architectural applications. The digital master model of some
ancient building - informed by archeological evidence and proposed restorations - may be designed anywhere on the globe, then
transmitted by extranet to the client's build-chamber. The EcoMarble project, for example, achieved a similar
museographical objective, apart from procuring replica consumer items. It involved the digitisation of classical statuary with a
3-D Laser-scanner, the construction of computer models, and the fabrication of artefacts from powdered marble using ProMetal technology.
Full scale freeform architectural components and surface structures have been produced at less than traditional manufacturing costs
especially if needed for a short end-product run. Specialized programs like MAGMASoft can aid the designer by predicting the cast
integrity (and hence structural suitability) of any metal dimensions, while iterative adjustments of one such part in a CAD layout
automatically propagate to the parameters of dependent structures.
Author: Marcel Ritschel, Date: 20 August, 2004 (revised: 2013)
Assignment for Design Computing and Digital Media
University of Sydney, Faculty of Architecture
6 Bibliography
3DPTM Laboratory MIT: 2000, June 28, What is the 3DPTM Process? Retrieved August 06, 2004 from: http://anxiety-closet.mit.edu/afs/athena/org/t/tdp/www/whatis3dp.html
3D Systems: 2003, 3D Systems. Retrieved August 12, 2004 from: http://www.3dsystems.com/company/index.asp
Ashley, S: 1995, Rapid Prototyping is Coming of Age, Mechanical Engineering 117(7): 62-68.
Brown, DC: 1998, Intelligent Computer-Aided Design, JG Williams and K Sochats (eds), Encyclopedia of Computer Science and Technology.
Chuk, RN and Thomson, VJ: 1998, A comparison of rapid prototyping techniques used for wind tunnel model fabrication, Rapid Prototyping Journal 4(4): 185-196.
Giannatsis, J and Dedoussis, V and Karalekas, D: 2002, Architectural scale modelling using stereolithography, Rapid Prototyping Journal 8(3): 200-207.
Park, B: 2003, February 28, Project: SDM, Rapid prototyping Laboratory Stanford University. Retrieved August 06, 2004 from: http://www-rpl.stanford.edu/research_detail.asp?ArticleID=3&ArticlePage=1&ProjectID=1
Stratasys: (N.D.), Stratasys in-office Rapid Prototyping Systems. Retrieved August 12, 2004 from: http://www.stratasys.com/site/sys_main.html
Z Corporation: (N.D.), Z Corporation. Retrieved August 17, 2004 from: http://www.zcorp.com/applications/applications.asp?ID=18